Lockout Tagout for (Compressed Air) Pipes: Tips and Tricks
- Posted on
- Posted in Lockout-Tagout
- 0
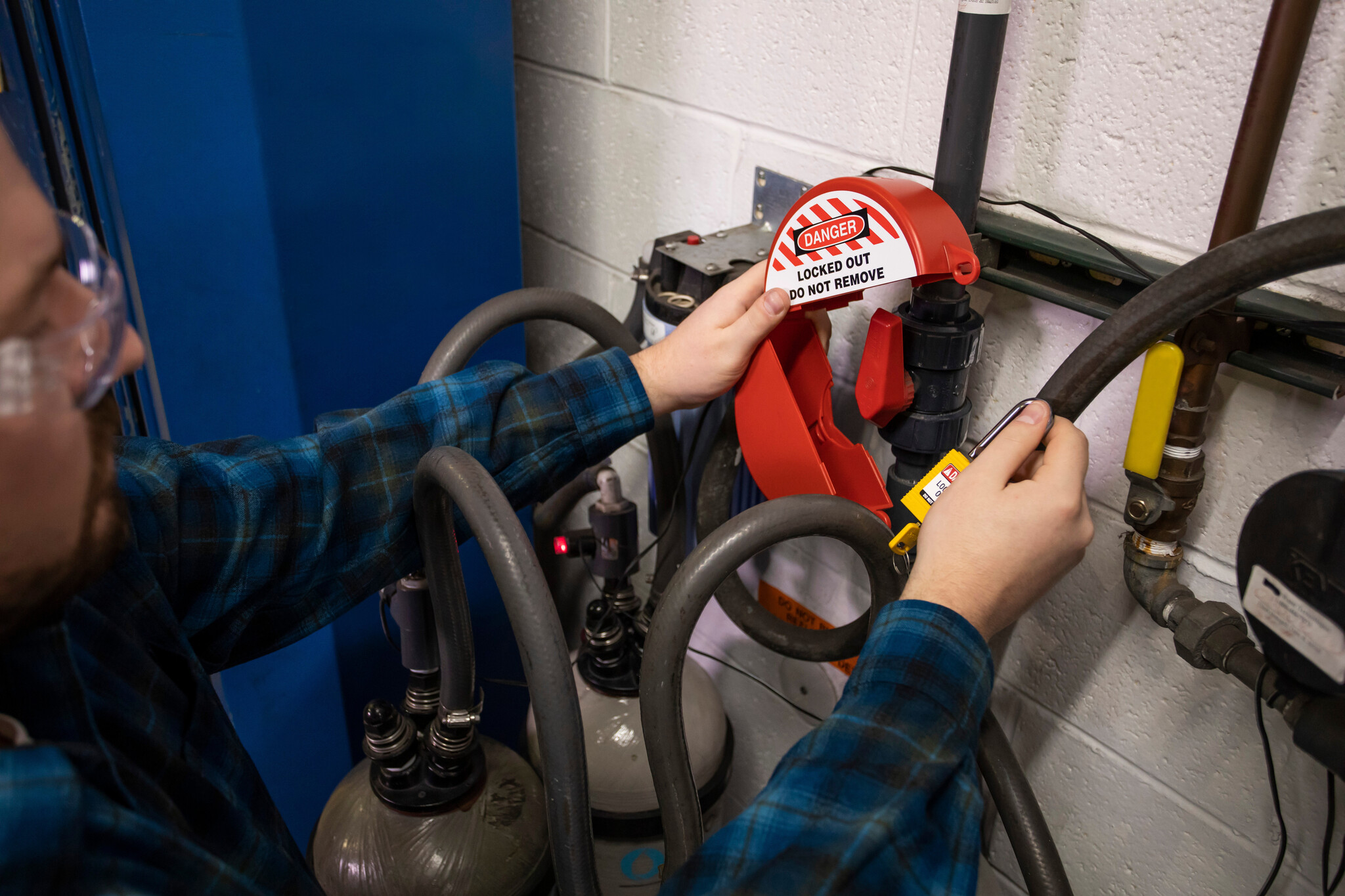
Safely locking compressed air lines and equipment, such as ball valves and butterfly valves, is essential to ensure worker safety during maintenance and repair work. Accidents resulting from unintended release of compressed air can cause serious injuries and even be fatal. Therefore, it is crucial to implement and strictly follow effective locking procedures. We offer a number of practical tips and guidelines for safely locking ball valves and butterfly valves in compressed air systems, enabling companies to minimise risks and ensure a safe working environment for their staff.
Various lockout-tagout devices are available for (compressed air) piping:
Lockout tagout for butterfly valves
A lockout tagout for butterfly valves locks valves in the open or closed position. It can be locked with up to two padlocks, or more in combination with a padlock bracket/padlock multiplier. These locking systems have an innovative design and are specifically developed for locking butterfly valves with the handle in the closed or open position.
Lockout tagout for ball valves
There are several types of lockout-tagout interlocks for ball valves, including ball valves without a handle, ball valves with a T-handle, and ball valves with a rotary knob. For the latter two types of ball valves, valve latches are available. These fully encompass the valve handle to prevent accidental operation of the handle, thereby triggering the valve. Locks are also available for ball valves without a handle. These cover the tap spindle for safe locking, effectively neutralising a machine's energy supply during maintenance operations.
In addition to selecting suitable locking systems, it is vital to follow the following guidelines:
- Identify all power sources before you start locking, including compressed air lines, electrical power supplies and hydraulic systems.
- Follow locking procedures established by your company or prescribed by relevant safety regulations, including the use of locking devices and tags.
- Use specific locking systems designed for ball valves and butterfly valves, such as clamp locks, padlocks and locking reels.
- Isolate compressed air lines by sealing them and releasing pressure before starting locking.
- Place locking devices in such a way that they prevent the valve or tap from being opened or closed, and make sure they are securely and safely fastened.
- Check for double locking to ensure that there are no other energy sources that can activate the equipment.
- Provide training and awareness to all employees involved in locking compressed air lines and equipment, and clearly document the locking process, including who is responsible for applying locks and when they are applied.
- Conduct regular inspections to check that the interlocks are still correctly placed and that there are no signs of wear or damage to the interlocking equipment.
Additional tips and tricks to make locking pipes even safer and more effective:
- In addition to locking devices, use locking tags to clearly indicate who is responsible for locking and when the locking process has started. This helps maintain clear communication and responsibility during maintenance operations.
- Regular maintenance and inspection of locking systems are essential to ensure they function properly when needed. Check for wear, damage or corrosion and replace locking devices if necessary to ensure reliability.
- Consider using colour coding for locking systems to quickly identify which equipment is locked and which procedures are being followed. This can help reduce confusion and improve efficiency during maintenance operations.
- Develop a structured locking policy within your organisation that clearly defines procedures, responsibilities and required training. Ensure that all employees are aware of this policy and adhere to it.
- Ensure employees are regularly trained and certified in locking procedures to keep their knowledge up to date and ensure they are competent in locking equipment safely.
- Implement workplace supervision to ensure that locking procedures are followed correctly and that all safety regulations are followed. This can help prevent errors and minimise risks.
- Conduct regular reviews of the locking process and identify possible improvements or adjustments that can be made. Take employee feedback seriously and work together to continuously improve workplace safety.
By following these practical tips and guidelines, you can improve safety when locking ball valves and butterfly valves in compressed air systems, reducing the risk of accidents and promoting a safe working environment.
View lockout tagout interlocks on our shop
Comments
Be the first to comment...